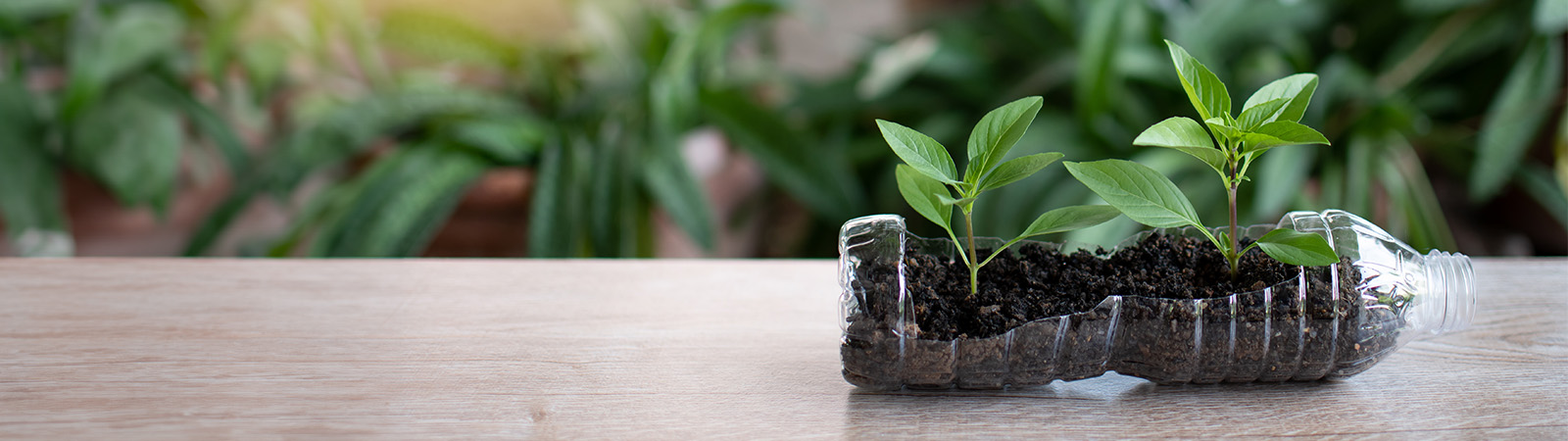
Recycling: Turning waste into resources
The Circular System of the Future
For Earth, for Life: Today, the Kubota Group's motto is more important than ever. Our planet is facing numerous challenges. Global warming, waste production, environmental pollution and resource depletion are among the problems that must be solved in order to ensure a future worth living for people all over the world. Recycling is a central component of the climate-neutral circular economy of tomorrow - and a basic building block of a sustainable society. Kubota Brabender Technologie offers feeding solutions for recycling processes of all kinds.
The Green Deal
We want the future of our world to be green. An important step in this direction is the EU's so-called "European Green Deal", which sets Europe the goal of becoming the first climate-neutral continent. In order to protect climate and environment, the EU member states are to reduce their net greenhouse gas emissions by 50 to 55% by 2030 - and achieve complete climate neutrality by 2050.
There is a lot to be done to make this happen. The energy transition and low-emission technologies are one pillar of the strategy; sustainable products and services are another. The industry must reduce its ecological footprint more and more and revise the raw material value chain with regard to sustainability and social impact.
The goal is a circular economy that encompasses even complex products like electric vehicles, clean technology and hydrogen plants. The recovery and recycling of critical raw materials plays a central role in making this goal a reality.
Circular economy: From cradle to cradle
In a circular economy, existing products are not thrown away, but repaired, reused, refurbished and recycled as long as possible. When a product has reached the end of its life, its materials are recovered and re-processed. This extends the product life cycle, minimizes the use of resources and reduces waste.
The "cradle to cradle" principle is a model for an efficient, sustainable circular economy. Nature – in which everything is a resource for something else - serves as the model. Like in nature, in a "cradle to cradle" economy, the waste of one system is the resource of another. Everything can be broken down into its component materials and reused – either as biological nutrients in biological cycles, or as technical nutrients in technical cycles.
Batteries: Building blocks for a green future
It is in high demand worldwide and electrifying in the truest sense of the word: the battery. Batteries are an essential source of energy in the modern world. They are also a key technology in the transition to a green future, not only – but also! - because as the heart of electric motors in vehicles, they are indispensable for the mobility transition to environmentally friendly transport. The global demand for lithium batteries is currently growing by 34 percent annually; by 2030, it is expected to increase more than eighteenfold.
In 2023, the EU put new regulations for batteries in place in order to minimize the environmental impact of this rapid growth. Batteries are to become sustainable throughout their entire life cycle, from raw material extraction to disposal, recycling and re-usage.
Recycling is a crucial step in this process. Batteries contain valuable and partly limited raw materials, including metals like nickel, cobalt, copper, zinc, aluminum and steel. Only modern recycling processes can meet the increasing demand for these materials in a sustainable and resource-saving way.
Die Dosiergeräte von Kubota Brabender Technologie unterstützen Recyclingprozesse, indem sie recycelte Materialien wie Kunststoffe und Fasern präzise dosieren. So wird Recycling effizienter und nachhaltiger.
Recovering limited resources
Recycling processes can already recycle up to 96 percent of the raw materials contained in used batteries and return them to the production cycle. This means resources are conserved, fewer raw materials are mined, and the industry's ecological footprint is drastically reduced.
The recycling of batteries is a very complex process. After the used batteries are safely collected, transported and sorted, they are crushed in special plants. The materials are then chemically or physically sorted. In the next step, they are recovered and made usable again.
Feeding the substances and chemicals used requires the utmost precision - particularly when it comes to sorting and recovery processes. In addition, batteries contain toxic and explosive substances that pose special demands and require a comprehensive safety concept. As an experienced partner of the industry, Kubota Brabender Technologie provides feeding solutions that optimally meet the requirements of battery recycling.
Mobility with a small ecological footprint
Valuable raw materials are not merely contained in the batteries powering the electric motors of tomorrow - to enable an environmentally friendly mobility solution, the vehicles themselves must also be integrated into the circular economy. For this reason, the EU regulation on the recycling of vehicles provides that at the end of their life, vehicles will become a source of spare parts, critical raw materials and important resources like recycled plastic and steel.
By effectively recycling decommissioned vehicles, the automotive industry is expected to achieve significant emission and energy savings in production by 2035. In addition, recycling will make 5.4 million tons of materials more available every year, and recovering critical raw materials ensures that the industry grows less dependent on imported primary raw materials.
Multi-talented plastic
It has long since become impossible to imagine our life without plastic. Its plethora of properties and applications make it almost omnipresent. More than 400 million tons of plastic are produced worldwide every year – and the trend is rising. A large part of this is used by the manufacturing industry in the form of packaging; construction, the automotive industry and the electronics industry are the next largest processors.
The impact of plastic on the environment is not fundamentally negative. On the contrary, plastic contributes to saving energy and resources and reducing emissions in various ways. Plastic packaging reduces food waste and significantly saves on materials compared to alternatives; due to its lighter weight, it also reduces the CO2 emissions caused by its transport. Weight-reducing components for cars and airplanes reduce energy consumption and emissions, and insulation materials for buildings allow significant energy savings. In medicine, plastic is helping to save lives and improve quality of life in many ways – and will do so to an even greater extent in the future thanks to 3D printing and biocompatible plastics.
Plastic recycling - the circular economy's priority
As of now, plastic production does not meet the requirements of a sustainable circular economy, especially when it comes to disposal and recycling. The associated environmental problems are severe. This is why plastic is the EU's main priority for implementing an effective cradle-to-cradle production. The largest share of plastic waste is generated by packaging; by 2030, all plastic packaging must be recyclable.
The recycling of plastic is as diverse as its forms. Depending on the application, recycling processes place very different demands on feeding devices – often under difficult operating conditions. They thus require flexible, versatile and durable feeders that combine precision and reliability with versatility. Kubota Brabender Technologie offers the right solutions.
Circular Plastics Alliance
In order to move the plastics industry towards an effective circular economy, more than 330 organizations from industry, science and public authorities have joined forces in the Circular Plastics Alliance. The Alliance has members along the entire plastics value chain and is committed to expanding the market for recycled plastics. As a first step, it aims to boost the EU market for recycled plastics to 10 million tons annually by 2025.
Feeding solutions for recycling processes
In addition to feeding recyclable materials, recycling processes often require the precise feeding of fillers, absorbents or reagents for the chemical separation, binding or cleaning of materials. The industrial operating environment is sometimes extremely harsh. Feeders from Kubota Brabender Technologie are integrated into numerous recycling processes worldwide - they offer the required precise weighing performance in combination with sensitive control technology and robust mechanics.
The feeding of long, heterogeneous fibers is a particular challenge. Such fibers are produced, for example, during the recycling of beverage cartons and building materials; conventional feeders cannot handle this material. However, thanks to its patented screw and trough geometry the FiberXpert fiber feeder, which is specially designed for such applications, can reliably pick up, guide and feed even irregular and non-flowing, easily interlocking fibers.
With regard to the circular economy of the future, the versatility and durability of Kubota Brabender Technologie's feeders are a particular advantage: not only are they extremely long-living, but they can also be easily converted and reused if the requirements of production change.