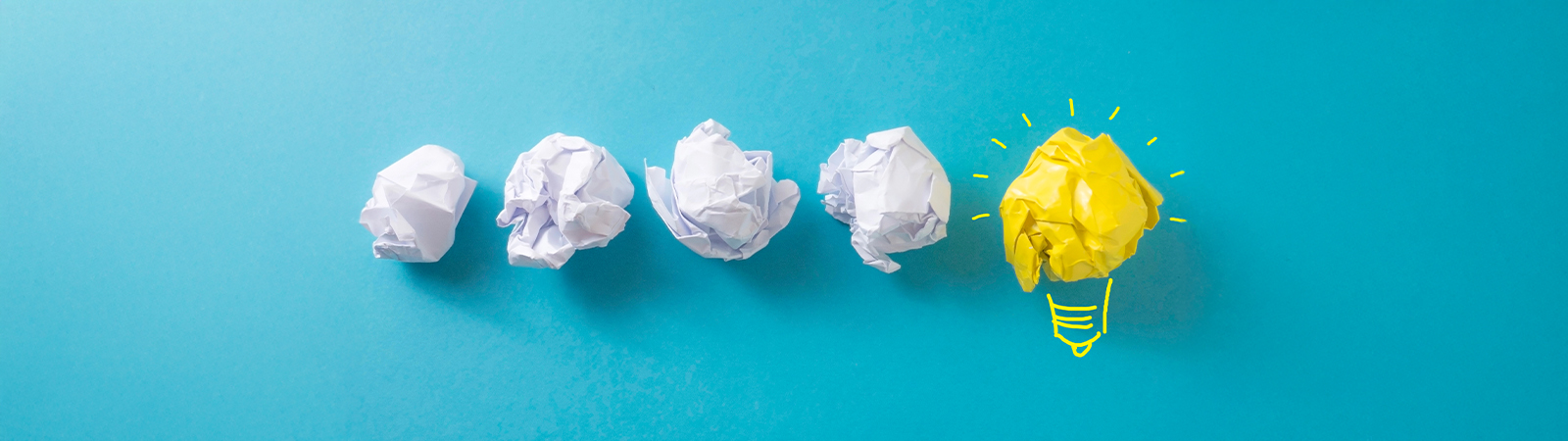
Idea management: Using ideas as a resource
Getting better together
What do reusable packaging for FlexWall® hoppers, printed spare parts labels and regular Mario Kart tournaments have in common? It's simple: all of them are based on good ideas from our staff. Kubota Brabender Technologie has dedicated and competent employees who think along; our idea management allows us to collect, evaluate and implement their valuable ideas for improvements.
"No one of us is as smart as all of us.” What author and entrepreneur Ken Blanchard succinctly summarizes is the concept behind idea management. We are constantly looking for ways to become more efficient, develop further and optimize our processes – and our employees' insights play an important part in this.
The high value of ideas
No one knows as much about our production processes, work flows and procedures as our employees. Kubota Brabender Technologie conducts idea management in order to utilize their detailed knowledge and creativity in a targeted manner. By collecting, evaluating and implementing their suggestions for improvement, we benefit from the insights and ideas our employees develop on the basis of their practical experience. Among other things, this allows us to improve company facilities, optimize organization, simplify processes, save resources and improve communication and occupational safety. Our experience with idea management has been extremely positive. Thanks to our intelligent and insightful workforce, we have received numerous valuable ideas over the years, allowing us to implement many positive changes.
Return system for reusable packaging
An excellent example of a significant positive change of this kind: the packaging return system we have developed with one of our suppliers. In the past, the housings and hoppers for our FlexWall® feeders were delivered to us wrapped in large quantities of plastic wrap and stacked on pallets. Not only did this result in a lot of plastic waste – the components were also not sufficiently secured against sliding.
An employee suggested a reusable system for packing the components instead, using precisely fitted packaging elements. The idea management team and the department management embraced this excellent idea, developed it further and were able to realize it in close cooperation with the supplier. Today, FlexWall® hoppers are fixed at the corners with custom-made, 3D-printed packaging elements, stacked on top of each other in a push-fit system and packed together on a euro pallet. The packaging elements are returned and reused and allow the components' safe stacking, preventing sliding or damage during transport. The new system offers greater stability and avoids significant amounts of packaging waste – a success made possible by the employee's brilliant idea and constructive cooperation with our supplier.
At the moment, we and another supplier are checking whether the system of reusable, fitted packaging elements is also suitable for packaging the double-shaft gearboxes of our DSR and DDSR feeders. The solution that has proved so successful with the FlexWall® cannot be implemented for all components – the sensitive load cells, for example, require special packaging measures for safe transport. For many other components, however, this system may be a viable future alternative.
Small component change – big effect
An employee's suggestion to adapt a pipe clamping set to make installation easier demonstrates how much a supposedly small change can achieve. As of now, technicians insert screws into the component from above and screw them in place with nuts at the bottom. However, due to the device's geometry, the space for this process is extremely limited – which means problems crop up again and again. At the suggestion of a technician, square and round holes will be swapped in future; the components will be manufactured in a way that allows screws to be inserted from below and easily fastened at the top. The result: increased productivity, more occupational safety and significantly less frustration for technicians.
Faster, cleaner, safer: connection cutting template
An employee who found cutting the flexible connections for our feeders' outlets too cumbersome not only suggested the solution, but also handled its technical implementation. The flexible connections are delivered by the meter; instead of continuing to measure and cut them individually, the inventive employee built a cutting device with a template. Now you simply place the length of tube on the template – and by closing the device, it is cut precisely to the required size. This excellent idea has significantly accelerated and simplified the process. Safety is not neglected either; the device is designed to ensure users cannot cut themselves with it.
Clever ideas for all departments
Our employees' suggestions for improvement relate to all topics and areas of the company. One significant change, for example, revolves around the bags used for shipping spare parts and loose parts like screws. Until a few years ago, employees labeled these bags by hand; now lists and labels are generated directly from the inventory management system and printed by means of a label printer. This saves a significant amount of time, is less error-prone and ensures a more professional external image.
In summer, at the suggestion of an employee, a special sun protection film protects employees in the production hall and offices from excessively bright sunlight and heat. And we now no longer buy sawdust to absorb oily stains, but use the shavings produced in the packing department when the shipping crates are sawn to size. This saves time and money in both purchasing and disposal. All that was needed was an adjustment in the company's workflows... and a great idea.
Team building with Mario Kart tournaments
Not all implemented ideas are strictly work-related. Once a quarter, the last Thursday of the month now turns into a Mario Kart tournament. After work, game-loving employees meet in the Duisburg meeting room. The game console is provided by an employee, and the powerful projectors that are usually used for meetings allow Mario, Luigi, Peach and Co. to cut an impressive figure on the racetrack. In a relaxed and informal atmosphere, the working day ends in good company – a fun way to bring employees from all departments together.
Collecting ideas
Kubota Brabender Technologie employees who have a suggestion for improvement can send it directly to the eight members of the idea management team by e-mail. There are also boxes set up in the production hall and foyer to collect ideas. Every suggestion should provide a brief but informative description of the problem and the proposed solution – including clarifying sketches or other documents. A particularly important point is that every submitted idea must describe not only a problem, but also a possible solution. Suggestions can and should go beyond the employee's own area of responsibility.
The path to implementation
Of course, not every suggestion can be implemented. Before a proposal is put into practice, it is reviewed and evaluated by the idea management team and the relevant specialist department. In addition to usefulness and practicability, important criteria include how well the proposal is worked out, how original it is and how far-reaching the positive consequences of the proposed change would be. Suggestions that improve employee safety or health are just as welcome as ideas that help protect the environment, increase productivity or work results, improve our public image or boost employee motivation.
If a suggestion is useful, practical and positive for the company, it only needs to be approved by management before it can be implemented. To acknowledge our employees' commitment, we award implemented suggestions according to the idea's impact: the greater the benefit, the higher the reward. In 2024, 28 proposals were submitted – 16 of them received a reward.
Commitment and inventiveness
It is extremely important to Kubota Brabender Technologie to create a positive working environment in which every employee is heard, recognized and actively involved. After all, companies are only as good as the people who work in them. This means we are particularly proud of our employees' commitment, expertise and inventiveness – qualities that are reflected in the 182 suggestions for improvement our idea management team has received since 2019.
How does idea management work?
Progress and innovation thrive on fresh ideas. But ideas alone are not enough to make real improvements possible – in order for good ideas to offer added value in practice, ideas must be systematically generated, collected, assessed, evaluated and implemented in a company. This is exactly what idea management does.