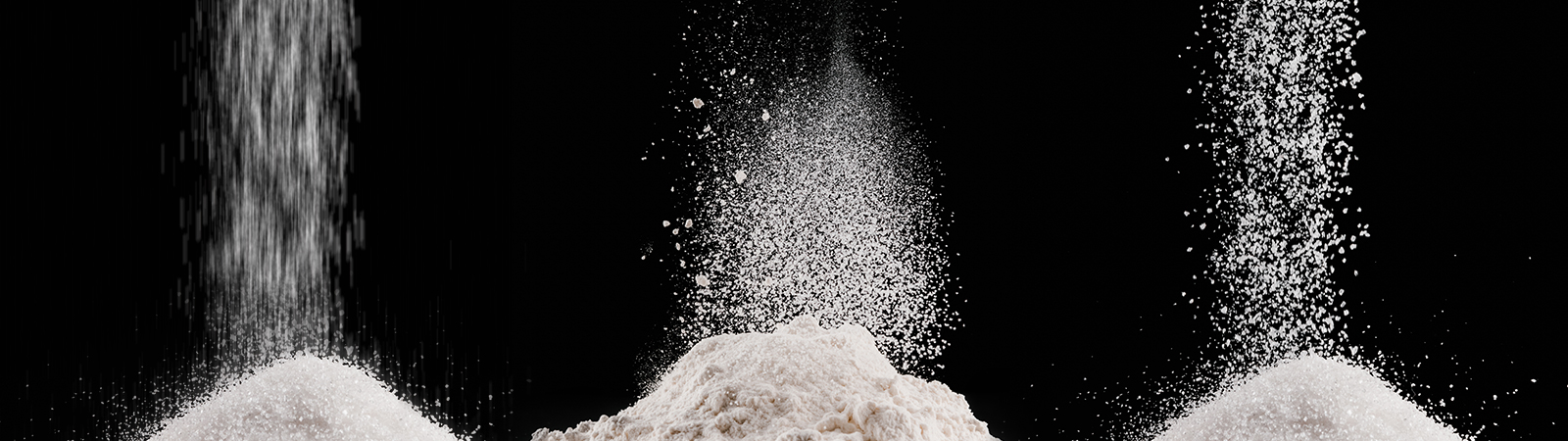
Refilling correctly – feeding reliably
When any unexplained process or torque anomalies occur, a check on whether refilling processes are being undertaken at the same time needs to be made. That is because they can sometimes have a serious impact on weighing results.
Filling and refilling processes can be accurately tested in Kubota Brabender Technologie’s Technical Center. “Many users underestimate how critical these processes are for weighing, especially during continuous production,” says Michael Richtmann, Head of the Service team at Kubota Brabender Technologie. That is why installation and maintenance or at least inspection of all the equipment should be undertaken by a single organization.
Possible causes of inaccurate weighing results during the refilling process:
- inadequate equipment support impacts on the weigh-feeder
- clogged filters prevent air escaping from hoppers
- a lack of seals in vacuum conveyors causes negative proessure
- components are not adequately maintained or cleaned
- refilling speed and quantity are too high
Structural stability impacts
We are familiar with this issue from our service visits”, says Michael Richtmann, talking from his team’s experience. “Customers often purchase feeders only and then incorporate them into their existing filling systems. In the case of large high-rate feeding equipment, a robust steel structure is sometimes integrated with the feeder system to support the weight of the equipment and bulk material. For example, when a bulk bag is emptied into a refill hopper, it generates a substantial dynamic force that can temporarily increase weights.”
Precision-feeding Anomalies?
Why not seek advice and avail yourself of the benefits of our Technical Centers worldwide:
This impacts on feeding accuracy. “Although steel is strong, it is also flexible. We can’t see it with the naked eye, but these vibrations can cause the discharge device to come into contact with the weighing unit. The scales feed in higher quantities, as they are measuring a gain in weight.” The screw’s rotational speed then increases as a result. “Customers then call to tell us that their feed rate is inaccurate. However, the fault lies in the structural design, because the feeder scales weigh more than just the bulk material.”
There must be greater focus on and increased customer awareness of that all-important refilling process.Michael Richtmann, Head of the Service team at Kubota Brabender Technologie
What venting problems can occur?
At a major customer event in Duisburg, engineers at Kubota Brabender Technologie set up three demonstrations of typical refilling problems. Inadequate equipment support was one of them, while another demonstrated a typical problem that occurs when powder is weighed. The problem was obvious – a feeder normally feeds powder very uniformly, however, the bulk material was discharged uncontrolled at high pressure out of the screw tube during refilling. What happened? The filter had clogged up and therefore the screw tube was the feeder’s only pressure release point. When the feeder’s hopper is filled, the displaced air needs to escape. It would normally escape via a filter outlet. If this is clogged, then the screw tube is the only remaining option for the air to escape, causing material to discharge in an uncontrolled manner.
“It’s something we come across again and again during our service visits: customers refill feeders very fast and in very large quantities to keep the volumetric feeding phase as short as possible during the gravimetric cycle”, says Michael Richtmann, talking from experience. “But they achieve exactly the opposite – there is a lot of air in a large empty feeder hopper and this air must escape during the refilling process. If the filter is undersized, the air pushes towards the only aperture, the screw tube,” the Head of the Service team explains. He suggests two possible solutions – either the filter needs to be cleaned regularly or a so-called JetFilter is utilized.
Self-cleaning JetFilter provides peace of mind
A JetFilter removes dust from the air that is displaced from the hopper during filling. In contrast to normal filters, it is also self-cleaning – it automatically cleans the filter with a pulse of compressed air that blows any trapped material back into the process. In a continuous process, jet filter cleaning occurs at the end of the refill, during the material stabilization phase without interfering with the gravimetric cycle. When very expensive or toxic materials are involved, the JetFilter is a must, but it can also be a good option for other powders and fine pellets. “The best thing for users to do is seek our advice”, Jochen Keesen, Head of the Technical Center, recommends. “We can help with selecting the right filter and determining cleaning intervals for normal filters.
Regular maintenance is key
On the third demonstration line, a feeder was attached to a vacuum conveyor. Both units are separated by a knife gate valve. “But this valve has to be monitored regularly and maintained”, says Jochen Keesen, who set up the demonstration. “Otherwise product residues or a defective seal could result in the valve not fully closing and thus leaving a small gap.” The vacuum conveyor then causes negative pressure inside the feeder, which has an impact on the scales. “As a result, the weight reading is reduced, because there is permanent upward suction.” This is displayed on the measurement screen as follows: the screw speed initially decreases briefly and then increases sharply, because this suction makes the hopper seem empty. Once the pressure evens out again, too much material is fed initially, because the screw speed is still too high.
Brochure Discharging and Refilling
You can find further information about our discharging and refilling solutions in our overview brochure.
Of importance to continuous production
The interest that many visitors showed demonstrates that Kubota Brabender Technologie had increased users’ awareness of “refilling” problems. “Continuous processes are becoming increasingly popular”, says Michael Richtmann. “That means also focusing on and increasing customer awareness of the refilling process.”