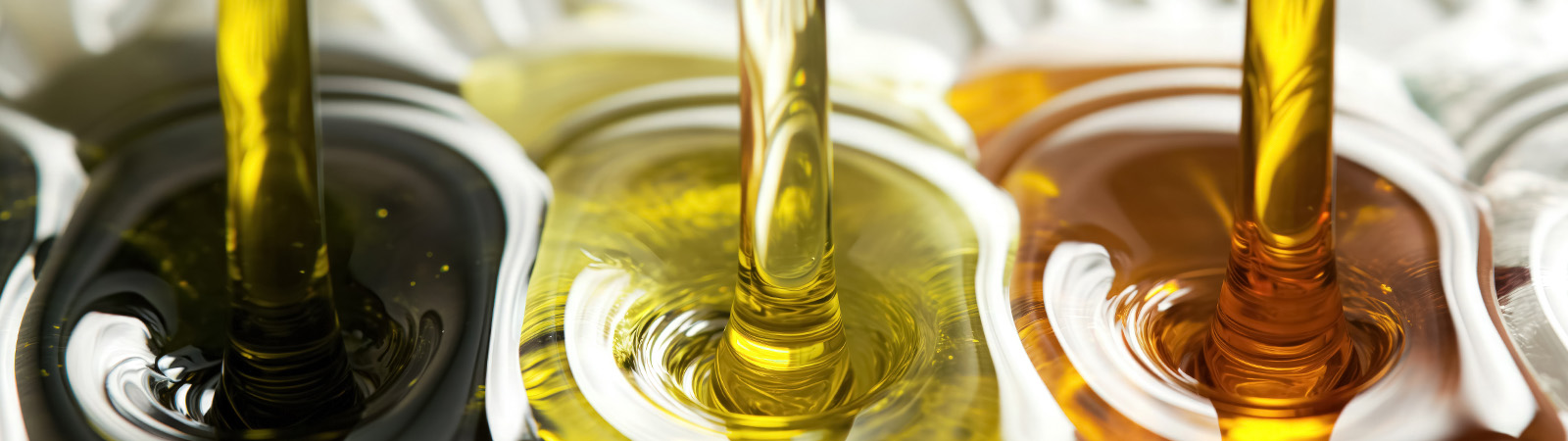
Feeding liquids: A complex and diverse task
Everything flows
From putting in contact lenses in the morning to driving to the office, doing the laundry after work, and relaxing on the couch with a snack: All day long, we are surrounded by products that are produced with liquids playing a leading role. The products in question are not merely "obviously" liquid ones like dishwashing liquid, shower gel, toothpaste, cough syrup or engine oil. Liquids of various kinds are also essential for the production of lithium-ion batteries, car tires, mobile phones, clothing, shortbread cookies, granola bars, chocolate, daily contact lenses, washing powders, and countless other things indispensable to our everyday life. To allow a consistently high product quality, all of these very different – and sometimes extremely demanding – liquids require precise feeding. A highly challenging task... and one that Kubota Brabender Technologie masters with flying colors, thanks to extensive experience.
The challenge of liquids
Panta rhei – everything flows. What Greek philosopher Heraclitus said about the constant change of material and form over 2000 years ago is Kubota Brabender Technologie's central task today. The feeding specialist keeps raw materials flowing so that production can run smoothly. The fact that liquids, of all things, pose a special challenge here may seem surprising at first glance. However, different liquids are characterized by extremely diverse properties – beginning, but by no means ending with their viscosity. In order to ensure that everything really does flow, feeders must be tailored precisely to suit the respective requirements. This is exactly what Kubota Brabender Technologie offers in the form of feeders for liquids that are custom-designed for the specific ingredient and application.
The supreme discipline of feeding
Liquids are true divas: Almost every one requires a very specific, custom-tailored treatment. Wax, for example, crystallizes and solidifies at room temperature; in order to remain liquid, it requires a constant higher temperature. MDI – an important raw material for the production of polyurethanes (PUR) – reacts with oxygen and must be isolated from the ambient air by suitable systems. The versatile silanes – which, among other things, connect materials as bonding agents or separate them by surface modification – cannot be allowed to come into contact with moisture. The all-rounder maleic acid, on the other hand, which is important for the plastics and pharmaceutical industries, is characterized by its special reactivity and chemical aggressiveness; processing it requires machines made of special materials. And these are just a few examples of the special treatments individual liquids require.
The central issue: Viscosity
One factor that plays an important role in the feeding of all liquids is their viscosity, or their thickness. The particles of more viscous fluids are bound together more tightly, making them less mobile; the higher its viscosity, the more resistant a liquid is to deformation. The spectrum ranges from compounds like solvents, which are much thinner than water, to very viscous materials like polyols, silicone oils, and printing inks.
What is viscosity?
- Viscosity is a measure of a liquid's "thickness".
- It results from the forces holding the substance's particles together.
- The stronger the cohesion, the higher the viscosity – and the thicker the liquid.
- Dynamic viscosity is usually expressed in millipascal-seconds (mPa·s) and measured by viscometers.
- Viscosity depends on temperature.
- The lower the temperature, the more viscous the liquid.
- Because of this, temperature must always be specified when measuring viscosity.
The influence of temperature
The viscosity of liquids is not a constant; it increases with decreasing temperature. Liquids are only fluid enough to allow feeding and further industrial processing within a certain temperature range. Water and other liquids that are low-viscosity at room temperature are uncomplicated when it comes to this. But matters are very different with other materials. They must be brought to a suitable temperature and kept there – while, of course, taking their other properties into account.
FDDW: Special solutions as the standard
Complex tasks require flexible solutions. Feeding liquids is an extremely complex task – and accordingly, Kubota Brabender Technologie's FDDW liquid feeder is one of the company's most flexible devices. Custom-made feeders are the standard here. In addition to the viscosity and correct temperature of the respective liquid, its density, solids content, reactivity, toxicological properties, and explosiveness, among other things, are taken into account in the development of the feeder.
Process requirements play an equally important role. Every feeder is designed to meet the needs of the respective manufacturing process in terms of accuracy and feeding performance as well as turndown ratio and counterpressure. For liquids with special requirements, the company provides – among other things – a system for N2 inertization, which uses nitrogen to allow the feeding of raw materials that cannot be allowed to come into contact with oxygen or moisture from the ambient air. Pulsation dampers ensure that sensitive liquids are fed out in a constant flow, without being subjected to pulsations or fluctuations. And as an alternative to gravimetric feeding, Kubota Brabender Technologie offers the Coriolis mass flow scale, which can be integrated directly into piping. It allows precise feeding at very high flow rates of more than 1,000 liters per hour.
There is an ideal system for all process requirements and product properties. Specific customer demands – such as cart mounting, additional ports and connectors for sensors, or special dimensions – are taken into account. In the case of entirely new requirements, the experts from Kubota Brabender Technologie work together with the manufacturer to develop the optimal solution. Thus, every FDDW device is not only precisely and customized to the raw material it is feeding, but also to the production process it is an integral part of.
The right pump
The pump is the heart of every FDDW liquid feeder. Piston diaphragm pumps are suitable for most low-viscosity liquids. This type of pump first generates negative pressure by the movement of a piston, which causes liquid to flow into the pump via the inlet valve, and then pushes it out of the outlet valve with positive pressure by the piston's countermotion. The liquid is separated from the pump mechanism by a diaphragm and does not come into contact with it; piston diaphragm pumps are thus also suitable for feeding many abrasive, aggressive or toxic fluids. Piston diaphragm pumps are recommended for devices that feed raw materials with a viscosity between those of water and olive oil – i.e., a viscosity of around 1 mPa·s to around 400 mPa·s.
Gear pumps are suitable for feeding honey and other liquids with a viscosity of around 300 mPa·s and higher. They are pulsation-free, characterized by robustness and high feeding accuracy, and have a high tolerance for pressure and heat. This type of pump uses two interlocking gears to exert pressure on the liquid to be conveyed.
Depending on requirements, other pump types are also used – for example, eccentric screw pumps can be a good choice for highly viscous materials like liquid paint. The focus is always on the specific application.
Safe and effective heating
Kubota Brabender Technologie provides suitable heating solutions for liquids that cannot be measured out or processed at room temperature. In the case of liquid heating by double-walled configuration, the entire structure of the FDDW feeder is double-walled, so that the raw material can be heated with water or thermal oil. This method provides constant heat and direct, uniform heat transfer up to 180°C. It is particularly suitable when waste heat from another process is available as a heat source; in addition, this heating system is suitable for explosion-protected, ATEX-compliant devices that process highly flammable or explosive materials and must be proofed against providing a potential ignition source. However, double-walled heating is not ideal for all applications. The screw connections create unavoidable, unheated dead zones, which can allow certain materials – such as wax – to harden.
The alternative system electric heating provides custom-made heat without dead zones via insulated, removable heating sleeves. Since each component has its own heating unit with this solution, different temperatures can be set if necessary – the piping can be heated more than the feeding unit, for example. Electric heating is not the optimal solution for ATEX-compliant devices, since proofing the heater against overheating as required is complex and cost-intensive. However, in non-explosive atmospheres, it can even be easily combined with a double-walled heating system. On an individual and application-specific basis – so that with this specific liquid and this production, everything flows.